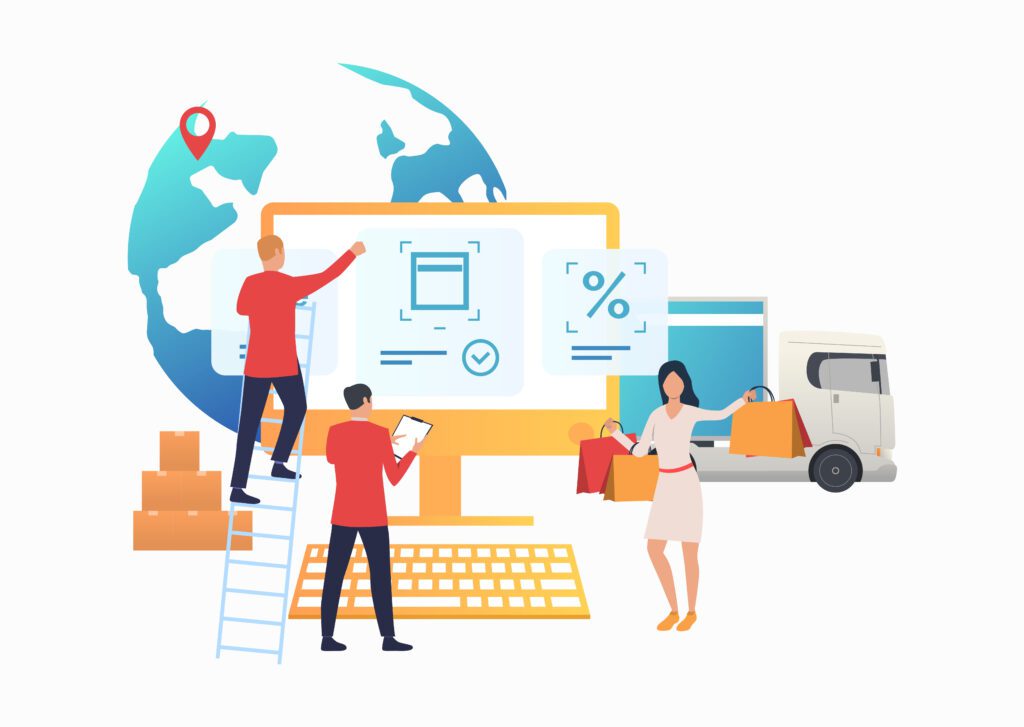
When you receive a purchase order, you’ll want to create a reallocating item procedure. This will describe the process of fulfilling sales documents and reducing inventory. This procedure should be set up to automatically handle all items when they’re allocated. Otherwise, the fulfillment process will simply take place when the items have been allocated. However, you can set up an override workflow so that it works for both processes. Here’s how to create a reallocating item procedure.
During Sales Transaction Entry, you can allocate items based on their line item, document, or batch number. You can also choose not to allocate items for an order. When you choose a quantity allocation option for an invoice ID, the amount allocated to each item will depend on the selection made during the order transfer. This way, you can handle quantity shortages as they arise. By default, this option is used for fulfillment orders.
After creating a reallocating item procedure, you can assign a new number to each item in the list. You can also assign a new number to a particular item. Then, you can re-allocate the items as necessary. You can change the allocation method in the Sales Automatic Order Allocation window. Then, you can select groups of documents and allocate items to them. Alternatively, you can set up a manual reallocating procedure for these types of documents.
You can also use the Reallocating Items Procedure to allocate document quantities. This can be done by selecting the allocation method for an order document. The process is automated, and you can use it to fill any sales order in your company. The number will be assigned based on the selection that you made during the sales transaction entry. During this step, you’ll need to assign the number of items based on their number in the sales order. You’ll also need to handle any quantity shortages that occur when you are handling orders.
Once you have the reallocating procedure created, you can allocate the documents based on the quantity. For instance, if you have a purchase order with a quantity shortage, you need to create a purchase order for that item. This procedure will help you to deal with quantity shortages as they occur. It’s also necessary to create a duplicate of an existing order for the same reason. You’ll need to use it to make a copy of it in case it’s not filled out properly.
Once you’ve created a Reallocating Items Procedure, you can assign it to your sales order documents. The procedure will allocate items by batch, document, and line item. For example, if an order contains a kit, you can allocate an item to a sales order that contains that product. Similarly, if an order has an order with an item shortage, you can set a batch allocation procedure to allocate the items to the kit.